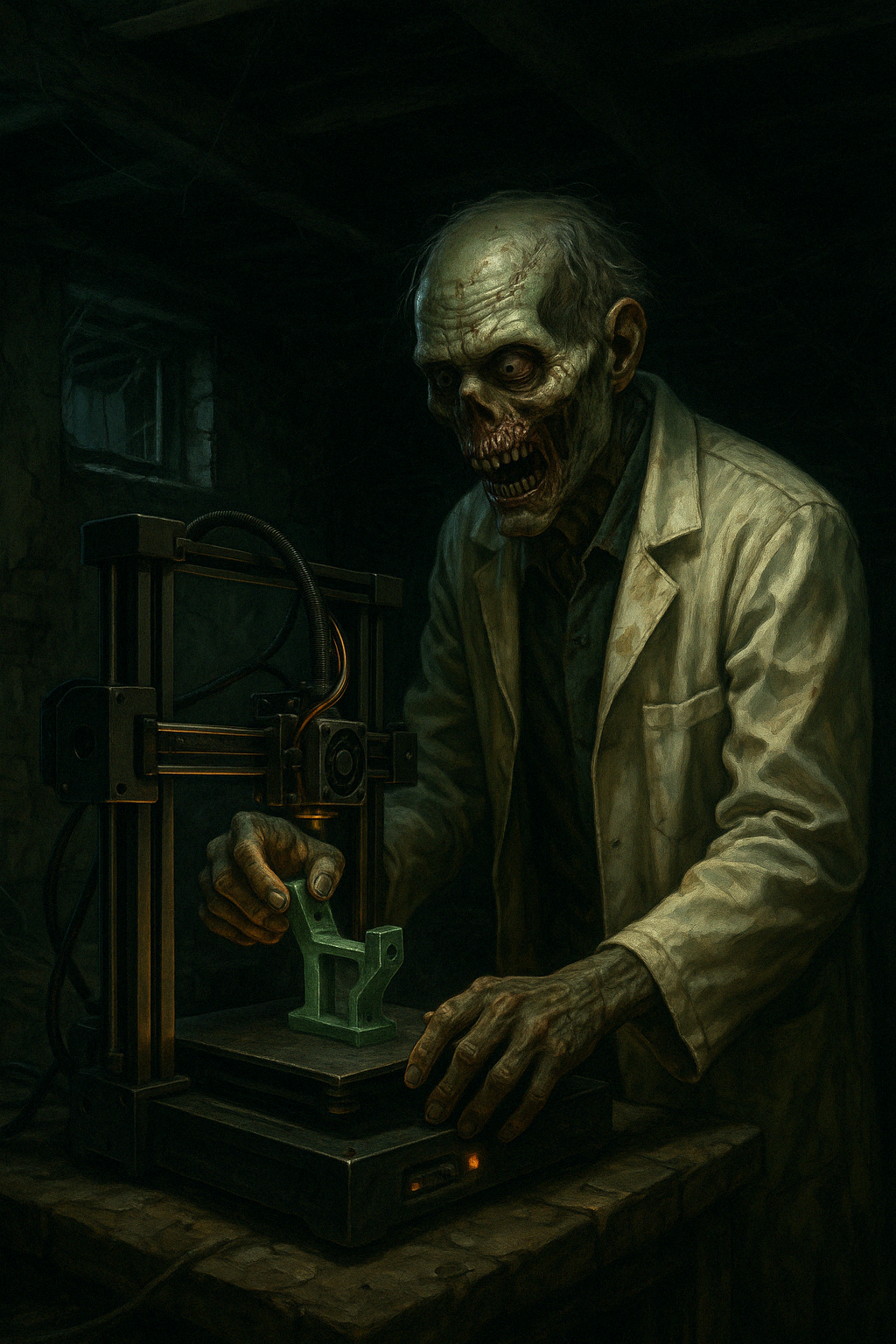
3D Printing
Additive learning. The only way to learn is by doing it. Here is what I know.
Additive learning. The only way to learn is by doing it. Here is what I know.
I started out with a cheap FlashForge Adventurer 3. The machine was only good for PLA prints and was too small for many of my projects. Later, I switched to an Ender 5. It couldn't make that machine print correctly if my life depended on it. The learning curve was too high.
My next upgrade was to the Adventurer 4. This was an easier transition; however, bowden style printers struggle with TPU. The hot end couldn't get hot enough for nylons and the required slicer software had huge limitations compared to Cura.
I then took a chance on AnyCubic Kobra. It was an open frame direct drive printer with PEI magnetic sheets and an auto-leveler. This machine is amazing. With a cheap enclosure and glue sticks, I am able to print just about anything. Nylon is a little out of reach because the hotend is at the edge of nylon required tempuratures.
Using Teaching Tech, I was able to print calibration cubes, temp & speed towers, and dimensional accuracy models to dial in any filament for perfect prints. It was like turning a corner. I was at a place where I could consistently print with success.
Next came designing things to print.
FreeCAD is a complicated program with awesome set of extensions.
The fasteners extension allows me to drop in industry standard screws, bolts, and nuts.
You can easily make basic shapes.
Cut shapes out of other shapes and round or chamfer the edges.
There is a feature called spreadsheet
which allows you to name cells and use them in part dimensions.
It was an absolute game changer.
I love designing and building practical things. The ability to dream up something and make a tangible item is like magic. The road is challenging. The rewards are worth it.
There are entire communities focused on printing firearms. I have seen some awesome builds; however, my experience is that it is not worth it. The gun part kits for 3D printed firearms are over $300 dollars.
AR-15 stripped lower receivers are $30 with FFL fee about ~$80. A complete lower parts kit is under $100. Complete uppers start at $250. So $450 gets you an all metal rifle good for 20 thousand rounds if maintained.
There are awesome budget pistols under $300 by major firearm companies with reputations for quality.
You will spend a huge amount of time making something that will fail. If you want to make firearms consider 80% lowers and desktop CNC machines. Nothing beats metal.
My advice is to focus on printing bows, crossbows, and slingshot devices instead of firearms. It gives you the flexibility to design, create, and share your builds without any potential legal issues. Reusable projectiles is fantastic.
I design alot of AR-15 related accessories like flashlight mounts and wall mounts. It saves me alot of money without scarificing weapon dependability.
Before diving into calibration and materials, selecting the right 3D printer is critical. Here are key factors to consider:
You want a direct drive all metal hotend.
Useful for high-temp materials. Keeps ambient temp stable and reduces warping.
Essential for materials like ABS that release fumes. Use filters or vent outside.
Some filaments (PETG, Nylon, TPU) absorb moisture. Use dryers or sealed storage with desiccant.
Glue sticks are a common adhesion solution. Alternatives include PEI sheets, painter's tape, and Magigoo. Clean the bed often.
Prints segments at different temperatures to find the best adhesion and finish.
Used to determine the ideal print speed for quality and strength.
Print test cubes or shapes to check for scale deviations. Adjust steps/mm or flow as needed.